For your information
You are being redirected to one of our divisional subsites which contains more detailed information on the required division. To navigate back to the main Invicta Group site, please click the link found in the footer at the bottom of the page.
- Systems
Systems
- Expertise
Expertise
-
Applications
- Archive Mezzanine Floors
- Art Gallery Mezzanine Floors
- Commercial Mezzanine Floors
- Data Centre Mezzanine Floors
- Factory Mezzanine Floors
- Laboratory Mezzanine Floors
- Mezzanine Floors For Manufacturer Storage
- Mezzanine Office Floors
- Outdoor Mezzanine Floors
- Production Mezzanine Floors
- Retail Mezzanine Floors
- Storage Mezzanine Floors
- Warehouse Mezzanine Floors
- Services
-
Applications
- Projects
- Insights
Insights
-
Articles
- How to elevate your retail business with a mezzanine floor
- 6 ways mezzanine floors can enhance your warehouse space
- UK mezzanine floor regulations: everything you need to know
- How to operate mezzanine floors safely
- How To Make The Most Of Your Startup Office Space
- 5 Things To Consider Before Starting Your Mezzanine Project
- Frequently Asked Questions
- A to Z of Terms
-
Articles
- Contact
Contact
UK +44 1843 220 256
US +1 305 328 9444
UAE +971 4 277 6225
Qatar +974 4441 4340
India +91 99 0355 9793
Malaysia +60 16 286 6225
- Start your project
How mezzanine floors are supporting multi-storey warehouses
14th May 2024
Quick Quote
Contact Mick Coyne
To get a quotation or arrange a free site survey - Call Mick Coyne on
-
UK
Current location:
Quick Quote
Contact Mick Coyne
-
UK
Current location:
In an era defined by rapid urbanisation, space has become a luxury in many countries. Cities are getting denser, rents are skyrocketing, and land for new builds is at a premium. Yet at the same time, the expectation of next-day and same-day deliveries is growing among consumers, creating a headache for logistics companies.
Serving this demand in a period of skyrocketing ecommerce demand requires increasingly innovative solutions, whether that’s drone deliveries or warehouse robotics. One simple solution that’s growing in popularity is the multi-storey warehouse, and its unsung hero: the mezzanine floor.
The multi-storey revolution
Historically, warehouses have been sprawling single-storey structures spread across expansive plots of land. However, in cities where every square foot comes with a high price tag, this traditional layout is no longer viable. At the same time, the growing demand for same-day deliveries in major cities is requiring more inner-city warehouses to be built, stocking popular items that can be sent out at a moment’s notice.
The solution to this is deceptively simple: build upwards, not outwards. Multi-storey warehouses are now becoming the standard in many locations, providing similar storage capacity to a traditional warehouse over multiple floors. These vertical facilities can not only accommodate more goods, but their compact footprint also translates to a reduction in land costs, and their locations mean shorter transportation times in urban settings.
The multi-storey boom in Asia
Asia, with its burgeoning population centres and rapid urbanisation, was an early adopter of multi-storey warehouses. Densely-populated countries such as Japan, South Korea, and Singapore faced unique challenges long before the rest of the world. Limited space, escalating property prices, and the rush to support booming e-commerce and manufacturing sectors compelled these nations to innovate.
In cities such as Tokyo and Shanghai, two of the world’s biggest metropolises, multi-storey logistics centres have become the norm rather than the exception. Singapore, with its limited land mass and thriving manufacturing sector, also became a hub for these vertical storage solutions. Early adoption and local development of robotics have helped to drive this development, improving picking and traversal times within these warehouses, particularly between floors.
There are a few obvious reasons why North America and Europe have lagged behind this trend. Both regions have historically had more sprawling landscapes, with ample space for single-storey warehousing. They have also benefited from robust and modern systems of roads and railroads crossing state and country lines, making horizontal distribution more viable for a long time.
There’s also the matter of cultural and architectural inertia. Western warehousing and industrial architecture have laboured to some extent under deeply ingrained ideas about space utilisation, both in terms of what was feasible and what was wanted by businesses. Changing such long-standing practices requires both a substantial amount of time and industry-wide impetus.
As urban spaces in the West have started feeling the pinch of escalating land costs and the pressing demand for faster logistics, however, the lessons from Asia are becoming more relevant. The rest of the world is now on the cusp of a multi-storey warehouse revolution, taking cues from its Asian counterparts, and infusing them with local innovation.
Mezzanines and multi-storeys
At the heart of this upward shift, both literally and metaphorically, is the mezzanine floor. While new inner-city warehouses may have multiple purpose-built floors, multi-tier mezzanines allow existing buildings to be easily converted into multi-storey warehouses. Mezzanine floors can also be easily modified or removed after installation, allowing businesses to customise the floor sizes and layout to meet evolving needs.
Compared to constructing an entirely new floor or expanding the building’s footprint, mezzanines offer a budget-friendly way to increase usable space within a warehouse. They can also be erected rapidly to ensure minimal downtime, something that’s crucial in an environment where work rarely stops.
Mezzanine floors using structural steel can be designed to support almost any load requirements, including large racking installations and heavy plant and machinery. They can also be equipped with safety railings, pallet gates, and conveyor systems to facilitate smooth operations, as well as a range of traversal options, from goods and personnel lifts to staircases and walkways.
Meeting urban demands
While the demand for urban warehouses is growing, it isn’t as simple as simply building warehouses in urban spaces. As well as the obvious issue of space – and how multi-storey warehouses have risen to meet this challenge – there are other logistical hurdles. Land prices and zoning issues present an immediate issue, while transport infrastructure has to be carefully considered. Multi-storey warehouses often require or benefit from multiple entrances, with direct access to each storey via lifts or ramps.
None of these problems are insurmountable, however. The advantage of mezzanine floors in particular is that existing buildings can be transformed into warehouses without substantially modifying the building structure. Transportation systems such as AS/RS and shuttle racking meanwhile can facilitate the use of multi-tier mezzanines and dense racking formats without requiring equivalent access to every floor of the mezzanine.
The benefits of urban warehouses, meanwhile, are clear. Located within city limits, these warehouses can dispatch goods far more swiftly than remote distribution centres, meeting the demand for same-day or even same-hour deliveries. Reduced transportation distances combined with smart routing also mean fewer emissions, supporting eco-friendly logistics. And by using smaller sites with vertical storage, the volume of goods that can be stored per square foot of land is maximised, resulting in better use of space and better ROI.
–
As urbanisation continues its relentless march, and e-commerce solidifies its dominance, the importance of multi-storey warehouses and industrial facilities is only going to grow. And given their myriad advantages, mezzanine floors are poised to be at the forefront of this architectural evolution. And who knows: with Amazon still experimenting with drone deliveries, the warehouse skyscraper could be a matter of months away.
Accreditations & Affiliations
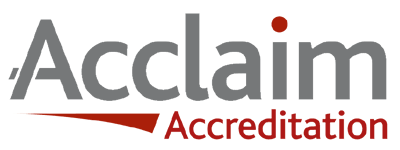
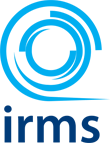
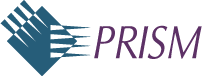
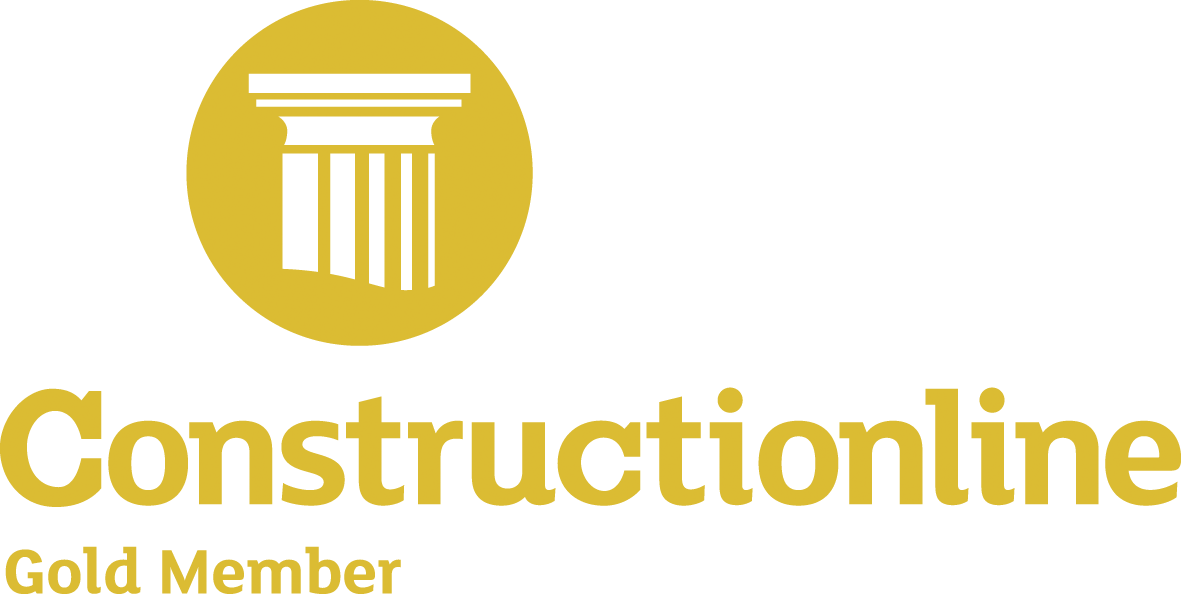
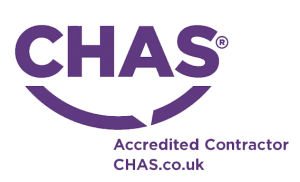
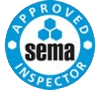
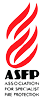
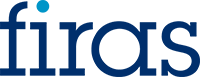
Start your project
Tell us about your project. Please complete this form. One of our sales team will come back to you with more details. If you prefer, you can drop us an email.
Share/Like this page